Accounting involves calculating work in process, which represents partially completed goods during a production period. For example, a furniture maker tracks the cost of raw materials, labor, and overhead allocated to unfinished tables.
Knowing how to calculate work in process is crucial for accurate financial reporting and decision-making. It helps businesses optimize production efficiency, manage inventory, and forecast future cash flows. Historically, this concept traces back to early cost accounting practices in the 19th century.
This article will provide a comprehensive guide to calculating work in process, including step-by-step methods and industry best practices.
Accounting
Work in process (WIP) represents partially completed goods during a production period. Accurately calculating WIP is crucial for financial reporting, decision-making, and optimizing production efficiency.
- Definition
- Importance
- Methods
- Benefits
- Limitations
- Historical Context
- Industry Best Practices
- Common Mistakes
- Software Solutions
- Case Studies
These aspects provide a comprehensive understanding of WIP calculation, encompassing its definition, significance, methodologies, advantages, constraints, historical evolution, industry standards, common pitfalls, technological advancements, real-world applications, and practical implications.
Definition
In the context of “accounting how to calculate work in process”, definition plays a critical role. It establishes the meaning, scope, and boundaries of WIP calculation, providing a clear understanding of its components and their significance. Here are some key facets of definition:
- Components of WIP: WIP encompasses raw materials that have been introduced into production, work in progress, and partially finished goods awaiting completion.
- WIP Valuation: Definition determines the methods used to value WIP, such as actual cost, standard cost, or a combination of both.
- WIP Measurement: Definition specifies the measurement techniques used to quantify WIP, including physical counts, production reports, and inventory records.
- WIP Classification: Definition clarifies the distinction between WIP and finished goods, ensuring accurate classification and inventory management.
Collectively, these facets provide a comprehensive definition of “accounting how to calculate work in process”, enabling businesses to establish consistent and reliable WIP calculation practices, make informed decisions, and maintain accurate financial records.
Importance
Precisely calculating work in process (WIP) is of paramount significance in accounting, impacting various aspects of business operations and decision making. It enables businesses to:
- Accurate Financial Reporting: WIP directly influences the calculation of cost of goods sold and ending inventory, ensuring accurate financial statements.
- Effective Inventory Management: Knowing WIP levels helps businesses optimize inventory, avoid overstocking, and prevent stockouts.
- Production Planning: WIP data aids in production planning, enabling businesses to adjust schedules, identify bottlenecks, and improve efficiency.
- Cost Control: WIP calculation reveals inefficiencies and areas where costs can be reduced, fostering cost optimization.
Overall, accurate WIP calculation provides valuable insights into the production process, supports data-driven decision making, and contributes to the overall financial health and operational efficiency of the organization.
Methods
Calculating work in process (WIP) is crucial for accurate financial reporting and decision-making. Various methods are employed to determine WIP, each with its own advantages and considerations.
- Actual Cost Method
WIP is valued based on actual costs incurred during the production period, including materials, labor, and overhead. This method provides the most accurate WIP valuation but can be complex and time-consuming.
- Standard Cost Method
WIP is valued using predetermined standard costs for materials, labor, and overhead. This method simplifies WIP calculation and reduces the risk of errors but may not reflect actual costs accurately.
- Equivalent Unit Method
WIP is valued by considering the equivalent units of production completed during the period. This method is used when different products are produced in the same production process and have varying completion stages.
- Weighted Average Method
WIP is valued based on the weighted average cost of units produced and in ending inventory. This method provides a more stable WIP valuation over time but can be less accurate than the actual cost method.
The choice of WIP calculation method depends on factors such as product diversity, production complexity, and data availability. Selecting the appropriate method ensures reliable WIP valuation, accurate financial reporting, and informed decision-making.
Benefits
Accurately calculating work in process (WIP) offers a multitude of benefits that enhance business operations and financial management. These benefits include:
- Accurate Financial Reporting
WIP calculation ensures accurate financial statements by providing the correct value of inventory and cost of goods sold, fostering transparency and reliability.
- Optimized Inventory Management
WIP data aids in optimizing inventory levels, preventing overstocking, reducing carrying costs, and ensuring availability of products to meet customer demand.
- Improved Production Planning
WIP information helps businesses identify bottlenecks, adjust production schedules, and improve overall efficiency, leading to increased productivity and reduced production times.
- Enhanced Cost Control
WIP calculation reveals areas where costs can be reduced, enabling businesses to minimize waste, improve profitability, and make informed decisions regarding resource allocation.
By harnessing the benefits of accurate WIP calculation, businesses gain valuable insights into their production processes, enabling them to make data-driven decisions, optimize operations, and achieve financial success.
Limitations
Understanding the limitations of calculating work in process (WIP) is crucial for accurate financial reporting and effective decision-making. WIP calculation involves inherent limitations that businesses must be aware of to ensure reliable information.
- Data Accuracy
WIP calculation relies on accurate data from various sources, such as production reports and inventory records. Errors or inconsistencies in these data can impact the accuracy of WIP valuation.
- Cost Allocation
WIP calculation requires allocating costs, such as overhead and indirect expenses, to partially completed goods. This allocation can be subjective and may lead to variations in WIP valuation.
- Product Diversity
In complex production environments with diverse product lines, calculating WIP can be challenging. Different products may have varying production processes and completion stages, making it difficult to accurately value WIP.
- Subjective Judgements
Certain WIP calculation methods, such as the equivalent unit method, involve subjective judgments and estimations. These judgments can impact the accuracy and consistency of WIP valuation.
Recognizing these limitations allows businesses to implement appropriate measures to mitigate their impact. Regular reviews, internal controls, and continuous improvement efforts can help ensure the reliability and accuracy of WIP calculations.
Historical Context
The historical context of calculating work in process provides valuable insights into the evolution of accounting practices and the significance of WIP in financial reporting. Understanding this context helps us appreciate the current methodologies and challenges associated with WIP calculation.
- Early Cost Accounting
WIP calculation has roots in early cost accounting practices during the Industrial Revolution. Manufacturers needed methods to track the value of partially completed goods and allocate costs accurately.
- Standardization Efforts
In the early 20th century, organizations recognized the need to standardize WIP calculation methods. This led to the development of standard costing and the concept of equivalent units, improving consistency and accuracy.
- Technological Advancements
Technological advancements, such as computers and specialized software, have significantly improved the efficiency and accuracy of WIP calculation. Automation has reduced manual errors and enabled real-time tracking of production data.
- Globalization and Supply Chains
Globalization and complex supply chains have introduced challenges in WIP calculation. Companies must consider factors such as intercompany transfers, foreign exchange rates, and varying production standards when valuing WIP.
The historical context highlights the continuous evolution of WIP calculation methods, driven by technological advancements, globalization, and the need for accurate financial reporting. It also emphasizes the importance of adapting WIP calculation practices to changing business environments and ensuring the reliability of financial information.
Industry Best Practices
In the realm of accounting how to calculate work in process, industry best practices constitute a set of guidelines and recommendations that serve as benchmarks for accurate and efficient WIP calculation. These best practices are shaped by the collective knowledge and experience of professionals in the field and provide a framework for organizations to optimize their WIP calculation processes.
- Standardization: Establishing standardized methods and procedures for WIP calculation ensures consistency and accuracy across the organization. This involves defining clear guidelines for data collection, cost allocation, and valuation techniques, minimizing the risk of errors and ensuring the reliability of WIP information.
- Regular Reconciliation: Periodic reconciliation of WIP balances with physical inventory counts is crucial to identify and correct any discrepancies. Regular reconciliation helps maintain the accuracy of WIP records and provides assurance that WIP is fairly stated in the financial statements.
- Cost Allocation Accuracy: Accurate allocation of costs, including overheads and indirect expenses, to WIP is essential for proper valuation. Industry best practices emphasize the use of appropriate cost allocation methods and regular review of cost allocation rates to ensure their accuracy and relevance.
- Technology Utilization: Leveraging technology, such as enterprise resource planning (ERP) systems and specialized WIP calculation software, can streamline and enhance WIP calculation processes. These tools automate data collection, facilitate real-time tracking, and provide robust reporting capabilities, improving the efficiency and accuracy of WIP calculations.
By adhering to industry best practices, organizations can enhance the reliability and accuracy of their WIP calculations, leading to more informed decision-making, optimized inventory management, and improved financial reporting. These best practices serve as a valuable guide for businesses seeking to establish a robust and effective WIP calculation system.
Common Mistakes
Common mistakes in accounting for work in process (WIP) can lead to inaccurate financial reporting, incorrect inventory valuation, and misguided decision-making. It is essential to understand these mistakes to avoid them and ensure the reliability of WIP calculations.
- Inaccurate Cost Allocation
Assigning incorrect costs to WIP, such as overheads or indirect expenses, can result in overstated or understated WIP values. This can have a ripple effect on cost of goods sold and inventory valuation.
- Incomplete Data Collection
Failing to capture all relevant data, such as materials used, labor hours, and machine usage, leads to incomplete WIP calculations. This can result in significant errors and misstatements in financial reporting.
- Inconsistent Valuation Methods
Using different valuation methods for WIP in different periods or for different products can lead to inconsistent and unreliable financial statements. It is crucial to establish and consistently apply appropriate valuation methods.
- Lack of Physical Verification
Failing to physically verify WIP inventory can result in errors in WIP calculations and inventory records. Regular physical counts help ensure the accuracy and reliability of WIP information.
Understanding and avoiding these common mistakes is crucial for organizations seeking to maintain accurate WIP records, make informed decisions, and ensure the integrity of their financial reporting.
Software Solutions
In the realm of “accounting how to calculate work in process,” software solutions play a pivotal role in streamlining and enhancing the accuracy of WIP calculations. These solutions are designed to automate various aspects of WIP accounting, from data collection and cost allocation to reporting and analysis.
- Data Integration: Software solutions seamlessly integrate with other enterprise systems, such as ERP and inventory management systems, to gather real-time data on production activities, material usage, and labor hours, ensuring comprehensive and accurate WIP calculations.
- Automated Cost Allocation: These solutions employ sophisticated algorithms to allocate overheads and indirect costs to WIP based on predefined rules and parameters, eliminating manual calculations and reducing the risk of errors.
- Real-Time Tracking: Software solutions provide real-time visibility into WIP status, enabling businesses to monitor production progress, identify bottlenecks, and make informed decisions to optimize production efficiency.
- Reporting and Analytics: The software generates customizable reports and dashboards, providing detailed insights into WIP trends, costs, and inventory levels, supporting data-driven decision-making and performance analysis.
By leveraging software solutions, organizations can significantly improve the accuracy and efficiency of their WIP calculations, leading to better inventory management, cost control, and overall financial reporting. These solutions empower businesses with the tools and capabilities to make informed decisions, optimize production processes, and gain a competitive edge in today’s dynamic business environment.
Case Studies
Case studies play a crucial role in the context of “accounting how to calculate work in process” by providing real-world examples and insights into the practical application of WIP calculation methods. They serve as valuable tools for understanding the challenges and complexities involved in WIP accounting, and for identifying best practices that can enhance accuracy and efficiency.
- Industry Examples
Case studies often showcase how different industries approach WIP calculation, highlighting the unique challenges and solutions specific to their production processes. This allows organizations to learn from the experiences of others and adapt best practices to their own operations.
- Benchmarking and Performance Analysis
By comparing their WIP calculation practices with those outlined in case studies, businesses can identify areas for improvement and set benchmarks for performance. This helps them optimize their WIP calculations and achieve greater accuracy in inventory valuation and cost reporting.
- Risk Mitigation
Case studies can help organizations identify potential risks and pitfalls associated with WIP calculation, such as errors in cost allocation or incomplete data collection. By understanding these risks and implementing appropriate controls, businesses can mitigate the impact of errors and ensure the reliability of their WIP calculations.
- Continuous Improvement
Case studies provide a platform for continuous improvement by sharing innovative approaches and successful strategies for WIP calculation. Organizations can learn from the experiences of others and adopt best practices to enhance their own processes, leading to increased efficiency and accuracy.
In summary, case studies offer valuable insights into the complexities of “accounting how to calculate work in process” by providing real-world examples, facilitating performance analysis, mitigating risks, and promoting continuous improvement. By leveraging these case studies, businesses can refine their WIP calculation practices, optimize inventory management, and enhance the accuracy and reliability of their financial reporting.
Frequently Asked Questions about Accounting for Work in Process
This section addresses frequently asked questions (FAQs) related to accounting for work in process (WIP), providing clear and concise answers to common queries and clarifying key aspects of WIP calculation.
Question 1: What is the purpose of calculating work in process?
Answer: Calculating WIP helps businesses accurately value and track the cost of partially completed goods during a production period, ensuring the reliability of financial statements and supporting informed decision-making.
Question 2: What are the common methods used to calculate WIP?
Answer: The actual cost method, standard cost method, equivalent unit method, and weighted average method are commonly used to calculate WIP, each with its own advantages and considerations.
Question 3: How does WIP calculation impact financial reporting?
Answer: Accurate WIP calculation directly influences the determination of cost of goods sold and ending inventory, which are crucial components of financial statements and affect the overall financial performance of a business.
Question 4: What are the challenges associated with WIP calculation?
Answer: Challenges include data accuracy, cost allocation, product diversity, and subjective judgments, which can affect the reliability and consistency of WIP calculations.
Question 5: How can technology assist in WIP calculation?
Answer: Software solutions can automate data collection, facilitate real-time tracking, provide accurate cost allocation, and generate comprehensive reports, enhancing the efficiency and accuracy of WIP calculations.
Question 6: Why is it important to regularly review and update WIP calculations?
Answer: Regular review ensures the accuracy and reliability of WIP information, identifies potential errors or discrepancies, and allows businesses to make informed decisions based on up-to-date data.
These FAQs provide a solid foundation for understanding the intricacies of accounting for work in process, highlighting its significance, methods, challenges, and the role of technology. The next section will delve deeper into the practical application of WIP calculation methods and industry best practices.
Tips for Calculating Work in Process
The following tips provide practical guidance to enhance the accuracy and efficiency of your work in process (WIP) calculations:
Tip 1: Establish Clear and Consistent Procedures
Develop standardized methods for data collection, cost allocation, and WIP valuation to ensure consistency and minimize errors.
Tip 2: Utilize Technology to Automate Processes
Leverage software solutions to automate data entry, cost allocation, and reporting, reducing the risk of manual errors and improving efficiency.
Tip 3: Regularly Reconcile WIP Balances
Periodically compare WIP balances to physical inventory counts to identify and correct any discrepancies, ensuring the accuracy of WIP records.
Tip 4: Allocate Costs Accurately
Use appropriate cost allocation methods and regularly review cost allocation rates to ensure that costs are assigned to WIP correctly.
Tip 5: Train Staff on WIP Calculation Methods
Provide training to ensure that staff understands WIP calculation methodologies and can apply them consistently.
Tip 6: Implement a Quality Control Process
Establish a system to review and verify WIP calculations, ensuring their accuracy and reliability.
Tip 7: Monitor WIP Trends and Analyze Variances
Regularly monitor WIP levels and investigate significant variances to identify areas for improvement and optimize production efficiency.
Summary:
By implementing these tips, businesses can significantly enhance the accuracy and efficiency of their WIP calculations, leading to improved inventory management, cost control, and financial reporting.
These tips lay the foundation for effective WIP calculation practices. The concluding section of this article will discuss advanced strategies for optimizing WIP management and its significance for businesses seeking to gain a competitive edge.
Conclusion
This comprehensive article has explored the intricacies of “accounting how to calculate work in process,” shedding light on its significance, methods, challenges, and best practices. A precise understanding of WIP calculation is paramount for accurate financial reporting, inventory management, and production optimization.
Key takeaways include:
- Accurate WIP calculation provides a clear picture of the production process, enabling businesses to make informed decisions.
- Various methods are available for WIP calculation, each with its own advantages and considerations, and the choice depends on factors such as product diversity and production complexity.
- Industry best practices, such as standardization, regular reconciliation, and technology utilization, can enhance the reliability and efficiency of WIP calculations.
In today’s dynamic business environment, effectively managing WIP is crucial for gaining a competitive edge. By leveraging the insights and strategies outlined in this article, organizations can optimize their WIP calculations, minimize errors, and make data-driven decisions that drive operational efficiency and financial success.
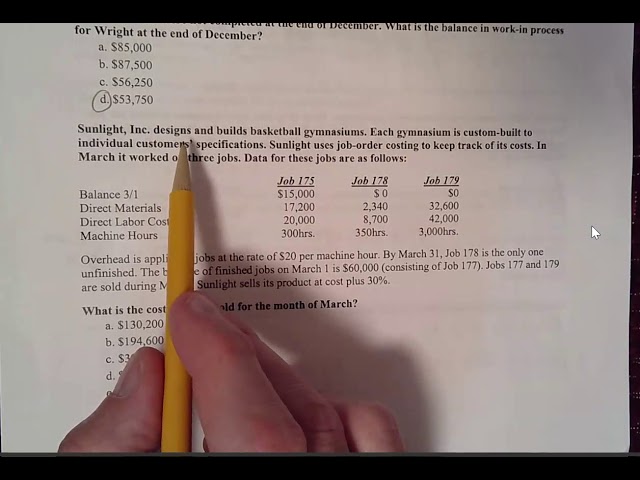